
AKTA Xpress Service & Repair
You rely on your equipment. Your equipment should rely on ATG.
Analytical Technologies Group are experts in service of the AKTA™ Xpress and other AKTA™ FPLC systems. We focus on maintenance and repair of only a narrow range of products, and thereby maintain expert knowledge on AKTA™ and other products which we service. We are able to accommodate urgent maintenance needs in most cases as we keep most components in stock.
With over 16,000 work orders successfully completed for over 1,000 different organizations, you can trust ATG for all your AKTA service needs.
Tips for keeping your AKTA™ Xpress in good working order:
The flow restrictor should be checked every month. Zero the pressure reading, then using deionized water, start a 5 ml/min flow from A1 to injection valve waste, then change the flow from A1 to outlet valve waste. The difference in pressure should be between 0.1 to 0.3 MPa. If it is not, the flow restrictor needs to be replaced.
Change the pump rinsing solution every week. The rinsing solution should be 20% ethanol in deionized water.
Periodically check the UV lamp run time. It is recommended to do so at least once every 6 months. At 254 nm, the lamp has a life of 7000 hours at standard room temperature or 2000 hours in a cold room. At 280 nm, the lamp has a life of 3500 hours at standard room temperature or 2000 hours in a cold room.
Keep the UV cell clean. A quick cleaning can be performed in place by running 1 M NaOH at 1 ml/min for 2 minutes, then leaving it filled with this cleaning solution for 30 minutes before flushing it with buffer or deionized water. Every six months, the UV cell should be taken offline and cleaned with 5 flushes of a 10% detergent solution then thoroughly flushed with deionized water.
The conductivity cell should be cleaned at least every six months by pumping 1 M NaOH at 1 ml/min for 2 minutes, leaving it filled with the NaOH solution for 15 minutes, then flushing with buffer or deionized water.
Keep the instrument itself and the area around it clean. It is far easier to keep the area clean than it is to troubleshoot and repair internal components when a failure occurs.
Having technical problems with your AKTA™ Xpress?
Fast Response
We provide very prompt responses to customers within one business day.
Fast Turnaround
Our field service engineers are expediently dispatched across North America & Europe to fulfill your service request.
Expert Staff
ATG’s highly trained, highly skilled staff ensure your instruments remain in optimal condition.
Parts In Stock
To minimize instrument downtime, we stock virtually all parts for the systems in which we specialize.
AKTA™ Xpress Troubleshooting Tips:
Most common measurement problems, such as baseline drift, ghost peaks, or general noise, are caused by the system being dirty or having air in it. A good first step to eliminate these causes is to clean the system and purge the lines. Degas all buffers before use. Centrifuge and / or filter your samples before loading.
High back pressure could be caused by clogging due to injection of dirty / unfiltered samples, using a high volume with a small column, a clogged online filter, injection of a highly viscous sample, or issues with the flow restrictor.
Sample loading failures are usually caused by air being introduced to the system during sample loading. Check the tubing and connectors, purge the pump, and ensure the flow restrictor is generating the appropriate 0.2 ± 0.05 MPa back pressure.
Low UV sensitivity may be due to an aging lamp, the UV lamp being in the wrong position, or the theoretical extinction coefficient of the protein being too low.
Drift in the conductivity measurement could be caused by changes in ambient temperature. As there is no temperature compensation, the measured conductivity will be different at different temperatures. Try to ensure the temperature in your lab is as stable as possible, and record the ambient temperature when performing runs.
If the conductivity value seems incorrect, it could be improperly calibrated. Recalibrate the conductivity cell and ensure the 1.00 M NaCl calibration solution is correctly prepared.
If you are having pressure or air problems and your buffer is thoroughly degassed, you may have a loose connection or other flow path problem. Check all connections for leaks. Ensure tubing is not kinked or twisted. Ensure the gel filtration column is in the left column holder so it does not impede the movement of the fraction collector.
Low buffer flow and a strange noise are telltale signs that a piston spring needs to be replaced in the pump.
Leakage around a pump head indicate that the piston seal or rinsing membrane either are installed improperly or need to be replaced.
Regardless of the problem, do not open the covers or separation systems. Accessing or replacing parts that are not intended for user manipulation should only be performed by trained service personnel.
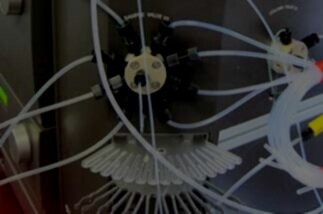