
ÄKTA ReadyFlux and ÄKTA ReadyFlux XL Service & Repair
Our team of experts at Analytical Technologies Group boasts an unmatched experience when it comes to handling different ÄKTA products like the ReadyFlux and ReadyFlux XL. If you are aiming for small scale single-use filtration, or manufacturing scale single-use filtration, or even both, we have you covered. At Analytical Technologies Group, we purposefully provide our clients with the maintenance and repair of only a narrow range of products, including the ÄKTA ReadyFlux and ReadyFlux XL, to ensure the finest quality of service on the market.
Having doubts? Ask the 4,000 customers ATG has kept satisfied. You rely on your equipment. Your equipment should rely on ATG.
Tips for keeping your ÄKTA ReadyFlux in good order:
Chemical stains and dust are removed by wiping the outside surfaces of the cabinet and the pump with a clean tissue wetted with water. 70% ethanol or 2-propanol (Isopropanol) can be used for sanitization.
If salt buffer is spilled on the valves, rinse carefully with water to remove salt crystals and wipe dry.
Clean the system of infectious or aggressive fluids before service or maintenance. Make sure that the cleaning procedure flushes all possible flow paths in the system.
To avoid corrosion, wipe the cabinet dry after cleaning.
Connectors on the cabinet, such as connectors for pH, conductivity, network, etc., that are not used, should be plugged to prevent cleaning liquid from entering the connector.
To avoid contamination, make sure the system is thoroughly cleaned before changing the flow kit.
After each run, clean the shaft of the feed pump P-201 after the flow kit has been uninstalled.
After each run, clean the rollers of the pumps P-202 and P-203 after the flow kit has been uninstalled.
Filters should be cleaned according to the instructions provided by the respective manufacturer's documentation.
Having technical problems with your AKTA™ ReadyFlux?
Fast Response
We provide very prompt responses to customers within one business day.
Fast Turnaround
Our field service engineers are expediently dispatched across North America & Europe to fulfill your service request.
Expert Staff
ATG’s highly trained, highly skilled staff ensure your instruments remain in optimal condition.
Parts In Stock
To minimize instrument downtime, we stock virtually all parts for the systems in which we specialize.
ÄKTA ReadyFlux and ReadyFlux XL Troubleshooting Tips:
If the “No air supply to the system” is displayed and the system raises a warning, check for leakage in the hose or a malfunction in the air supply equipment. If the air leakage sound is audible from inside the system, contact a Cytiva representative.
If “Valve Error” is displayed, a valve lock may be open; Check the valve locks and close if necessary. To close an open safety lock on a pinch valve:
1. Open the valve through system control or manual instructions.
2. Turn the black lever on the pinch valve 180 degrees to close the pinch valve lock.
3. Close the valve through system control or manual instructions.
If there is little or no flow in the feed pump, check that the connected inlet is used. If no liquid is supplied to the pump, check inlet containers. If P201_Gain factor is incorrect, check by setting default value.
If the Pressure Control Valve isn’t working, the valve may be open, the system might not be receiving proper air supply or the emergency button might have been pressed. If none of the above applies, contact Cytiva service personnel.
If the pressure monitors are giving incorrect readings, make sure that the pressure sensor cable is properly connected to the system cable
If there are errors in temperature readings, the system temperature might not be stable with respect to its surroundings. If the room temperature changes or if the system is moved from one room to another, it must be given time to adjust to current room temperature.
Facing technical problems with your ÄKTA™ ReadyFlux or ReadyFlux XL?
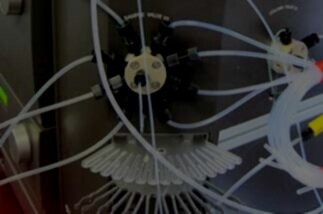